7 Tips For Choosing The Right End Mill For Your Work
Kategori: Allmänt
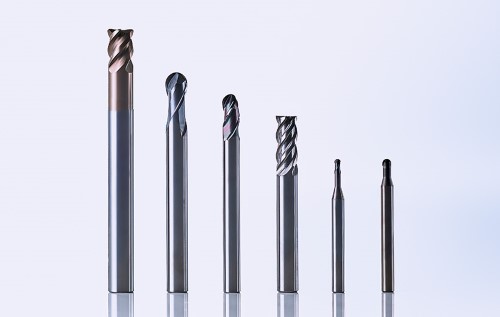
M&M Sales and Equipment offers end mills and accessories from Sandvik and Guhring. We also offer additional cutting equipment and accessories by Drillco, Guhring and Drillco. This is a comprehensive guide to end mills, and how to choose the most appropriate one for the job:
It's no secret that machinists tend to speak in their own language - even in something as simple as math. The rest of the world starts counting from the point 1. If you ask a machine operator to explain how they measure, and they'll tell that the process begins at one-thousandths of an inch (0.001").
If we are talking about cutting tools, it's pretty much the same thing. For the uninitiated, it can be difficult to understand the terminology of the term "machining. {For the rest of us it is clear that While the letters pcd diamond end mills are often used interchangeably to mean specific tools required for CNC machines, this could create confusion for people outside of the world. Industrial CNC (Computer Numeric Control) machines employ rotational cutting tools called end mills to remove materials.
What is an endmill and how is it different from drill bits? End mills are able cut vertically, while drill bits can be placed vertically in material to create holes.
Here's a good visual which demonstrates the distinction between a normal drill bit and an end mill:
Choosing the Right End Mill for Your Job
End mills are designed with the intention of achieving a specific purpose. Each tip provides a distinct clearing path for various uses. The details of the project and the material that will be cut, and the finish desired are all crucial when deciding which end mill to choose. An unsuitable tool can cause damage to your workpiece and cause you to have to throw away the entire batch. Not only is this a huge waste of time, but also a significant expense to your business.
There's plenty to think about when choosing the right end mill for your CNC. We've narrowed down a few important tips from Machining News to help you choose the best end mill.
End Mill Length
First, determine the length your end mill must cut. The endmill with the shortest length that is able to cut the job is the most efficient. What's the reason? The tool's stability is greatly enhanced by selecting the shortest length. This allows you to feed faster and more aggressively as well as reduce chatter.
End Mill Materials
High-speed steel (HSS) as well as carbide, are the two most widely used materials in the manufacture of end mills. HSS is a good choice for older machines which are slower or less rigid, or for production that is one-off or limited-run. Although it's slower than other materials, it is less expensive, less brittle, and is able to withstand instability better. Carbide is preferred in CNC machine tools that require greater speeds, less tooling change and greater productivity. In these instances the cost increase is easily justified by a longer tool lifespan and shorter cycle times.
Flute count
The flutes are the helical grooves that are wrapped around end mill set. For materials that require long-chipping, such as aluminum, a smaller number of flutes (between 2 and 3 flute tools) will provide more space for flutes. A higher number of flutes can reduce flute space but offer more productivity for shorter-chipping materials such as medium-to-high carbon iron or steel. A four-flute endmill is best for slotting stainless steel, high-temperature alloys and iron. It can also be employed as a general-purpose tool. More flutes should be reserved for applications with a low radial depth of cut in order to allow chip removal.
End Geometry
The success of the tool depends on your choice of the correct end mill. It is essential to know the types of materials recommended for the tool. The same is true for the speeds and feeds the manufacturer recommends for that material.
End Mill Coatings
Coatings can reduce friction and shield the carbide from heat generated during cutting. Certain coatings may be more appropriate for certain types of materials. It is essential to follow the manufacturer’s recommendations to ensure that you're using right coating.
The Life of the Tool
Cheaper isn't better. It's essential to use the proper tools for large-scale production and huge work loads. Making the wrong choice with inadequate or ineffective tools can cost both time and money in the form of wasted material, scrap, wasted tool spend as well as wear and tear on your CNC machines.